Diese Website verwendet Cookies, damit wir dir die bestmögliche Benutzererfahrung bieten können. Cookie-Informationen werden in deinem Browser gespeichert und führen Funktionen aus, wie das Wiedererkennen von dir, wenn du auf unsere Website zurückkehrst, und hilft unserem Team zu verstehen, welche Abschnitte der Website für dich am interessantesten und nützlichsten sind.
Das ist GRIBI 3D Druck
Unsere Showcases
Unsere 3D-Druckteile werden an den unterschiedlichsten Orten eingesetzt. Von der wandelbaren Uhr bis zur ultraleichten Drohne.
Showcases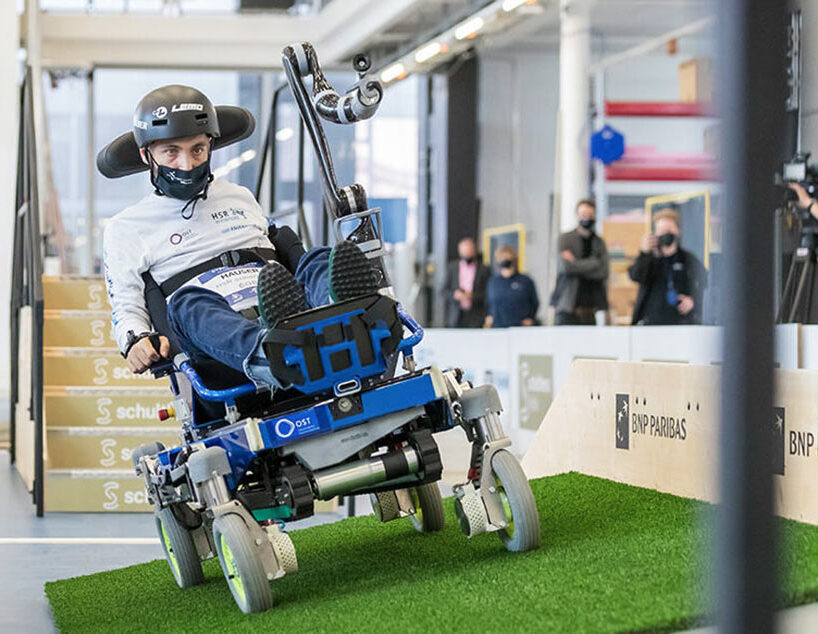
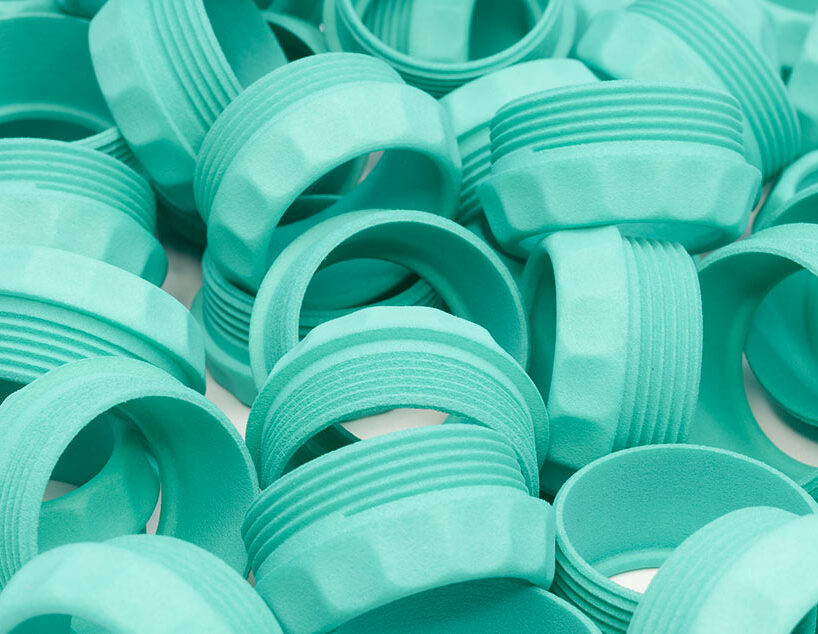
UNSER ANGEBOT
Wir sind spezialisiert auf den industriellen 3D-Druck. Dies erlaubt uns, hochkomplexe Bauteile innert kürzester Zeit zu fertigen. Vom Einzelteil bis zur Serienproduktion.
angebotÜber uns
Wir verwenden die neuste Technologie der Marktleader im Bereich industriellen 3D-Druck und arbeiten ständig daran, unsere Qualität weiter zu verbessern.
Unternehmen & Team
Schreiben Sie uns Ihr Anliegen per E-Mail.